Our automated ultrasonic passivation equipment using nitric or citric acid perform an automated process of cleaning-rinsing-passivation-rinsing-drying by moving the fluids from heated storage tanks into a single ultrasonic process tank, rather than moving the parts basket through a series of tanks.
With this passivation machine, the entire process required to clean, rinse, passivate, rinse, rinse and dry manufactured stainless steel metal parts is performed at the push of a button using user defined cycles via touch panel screen. The process is PLC computer-controls the fill-and-drain sequence to cycle parts through the cleaning, rinsing, and hot air drying processes; all within a single chambered unit.
Ultrasonic Automated Passivation Equipment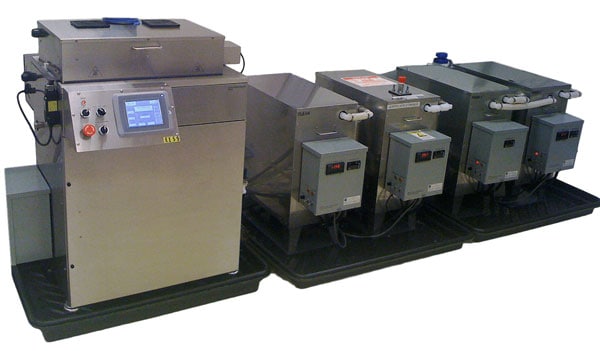
Video: Automated Ultrasonic Passivation Equipment for Citric or Nitric Acid
Small Ultrasonic Automated Passivation Equipment
Modular heated storage tanks complete the Ultrasonic cleaning machine for re-use of detergents and rinse water. This system configuration removes operator interaction, variability and eliminates exposure to chemicals. The end result is higher quality cleaned and passivated parts with tighter process controls which can be easily validated for regulated products like medical device and aerospace. The operator simply puts dirty, dry parts in, hits start and returns to cleaned, passivated and dry parts.
Need More Throughput?
Dual Ultrasonic Automated Passivation Equipment
Double production without doubling the cost. Learn how a dual process unit automated ultrasonic passivation system can boost your production. The model shown here features optional rotating baskets for parts.
We move the fluids NOT the parts! Savings of nearly 50% of system cost over traditional multi-tanks with overhead basket carrier automation.
Video: Automated Customizable 3-in-1 Nitric and Citric Passivation System
Need BOTH nitric AND citric acid passivation? This system can handle it all. This 3-in-1 system offers 3 different automated passivation options:
- Nitric acid
- Nitric acid with sodium dichromate
- Citric acid
Automated Passivation FAQs
-
Why are automated systems easier to process validate than manual equipment?
Process control and stability are critical aspects to regulated medical device and aerospace processes. It is important to ensure that a process has input and output variable limits which are defined and fully tested during process design, Equipment Qualification (IQ), Operational Qualification (OQ) and Process Qualification (PQ) validation testing. Setting up a proper DOE (Design of experiments) to test these limits is also important as the results of the DOE will give statistical confidence intervals of the limits.
Being that operators and employees perform various process operations different no matter how instructed in work instructions, the variation of operators must also be captured during process qualification (PQ) validation. An automated system typically eliminates many of the operator variability in the manufacturing process and this process “input” elimination also allows for tighter process output controls.
For example, in our automated passivation system, the elimination of relying on an operator to move the parts basket from stage to stage ensures that the parts remain in the appropriate (wash, rinse, acid passivation, etc) solutions for the process defined times and in accordance with the proper ASTM A967, AMS2700, etc specification. If a parts basket is immersed in the acid passivation solution too short or long duration, the passivation can likely fail and be outside specification limits.
-
Do you need any agitation beyond ultrasonics during the cleaning or passivation process with an automated system?
Our automated cleaning and passivation system includes in-process tank circulation which agitates the solution, alternating between ultrasonics (as fluid movement dissipates ultrasonic energy). This also allows the process tank to filter solution back in the storage tank.
-
In an automated system, are there contamination issues when you pump solutions out of the main processing tank?
Many of our automated cleaning and passivation systems pump the cleaning, rinsing and passivation acid solutions between tanks, unlike a traditional system where the parts are moved from tank to tank.
To reduce any contamination issues, we mount rinse spray nozzles in the cover of the system to rinse down the parts and tank walls. All the plumbing to and from the process tanks is separated to further reduce any contamination. This results in less contamination compared to the drag-out that occurs from moving parts from tank-to-tank in a traditional multi-tank setup.
-
What is the industry standard for acceptable particle count after cleaning or passivation?
Acceptable particle counts depend on the specification which the parts are processed to: ASTM A967, A380, F86, AMS 2700, etc. For passivation, DI rinse water is recommended for best results.
Our automated systems offer conductivity meters which monitor water quality and total dissolved solids. The storage tanks have facility DI water source needle valves which open when conductivity limits are not met. This allows for a continual overflow of the rinse tank until rinse water specifications are reached.
-
What are the pros and cons of pump-based systems vs. rail-mounted gantry crane automation?
Pump-Based System
-
Lower System Cost: Typically less expensive to purchase and install.
-
Simplified Maintenance: Fewer moving parts reduce the risk of mechanical failure and simplify upkeep.
-
Compact Footprint: Takes up less space on the production floor.
-
Flexible Tank Placement: Storage tanks can be located outside of the cleanroom or processing area.
-
Closed-Loop Operation: Minimizes operator exposure to chemicals, improving safety and compliance.
Cons:
-
Longer Cycle Times: Requires time to fill and drain the process chamber (typically ~2 minutes each).
-
Single-Basket Workflow: You must wait for the entire cycle to finish before processing the next batch.
-
Process Limitations: Not compatible with pickling or descaling applications.
Rail-Mounted Gantry Crane Automation
-
Higher Throughput: Multiple baskets can be processed in succession, increasing production capacity.
-
Scalable Design: Systems can be built much larger to handle high-volume needs.
-
Supports Pickling/Descaling: Capable of handling aggressive chemical processes.
-
Faster Cycles: No fill or drain steps—parts move through already-filled process tanks.
Cons:
-
Higher Initial Cost: Requires more infrastructure and automation.
-
Larger Footprint: Occupies more floor space compared to pump-based systems.
-
Increased Maintenance: More mechanical components introduce additional maintenance needs.
-
Common Applications for Automated Passivation Equipment
- Ultrasonic part cleaning and passivation of water soluble machining coolants, chips, particulate, and true machining/cutting oils, buffing and lapping compounds.
- Medical device stainless steel, titanium, tantalum parts cleaning and passivation
- Aerospace part passivation
- Nitric acid passivation type 1, 2, 3, 4 ASTM A967
- Citric acid passivation type 1, 2, 3, 4, & 5 ASTM A967 using CitriSurf® citric acid passivation solution
- General washing for maintenance, manufacturing, rework and/or remanufacturing.
- Applicable case study: Automated Ultrasonic Passivation System for Medical Device and General Parts
Learn more about automation benefits on our page What is Process Automation for Metal Finishing?
CitriSurf® is a registered trademark of Stellar Solutions, Inc. McHenry IL USA.
Typical Configurations
The automated passivation equipment configurations below are most common, but systems of any size from 3.5 to 100+ gallon and 1 foot to 15 foot long can be fabricated based on customer application for little to no custom costs. Systems can contain pH and conductivity meters to monitor wash, acid and RO / DI rinse solutions.
Model Series | Liquid Capacity (gallons) | Ultrasonic Power (Watts) | Hot Air Dryer (Watts) | Tank Dimensions (l x w x h) | Main Process Unit Dimensions (l x w x h) | Storage Tank Capacity (gallons ea) |
1002P | 3.5 | 300 | 1500 | 12″ x 10″ x 8″ | 24″ x 13″ x 18″ (tabletop) | 15 |
700P | 9 | 1200 | 3000 | 18″ x 12″ x 10″ | 28″ x 22″ x 39″ | 15-30 |
992P | 18 | 1800 | 3000 | 24″ x 14″ x 12″ | 28″ x 22″ x 39″ | 30 |