Heavy-Duty Passivation System
For passivation systems where high-volume production processing is a requirement, Best Technology is pleased to offer Automated Passivation Systems for High-Volume Production.
Our innovative gantry rail system, distinct from traditional overhead systems, integrates seamlessly with the tank line. This design saves valuable production floor space while enhancing operational efficiency and productivity.
Video: Rail-Mounted Automation Boosts Passivation Output
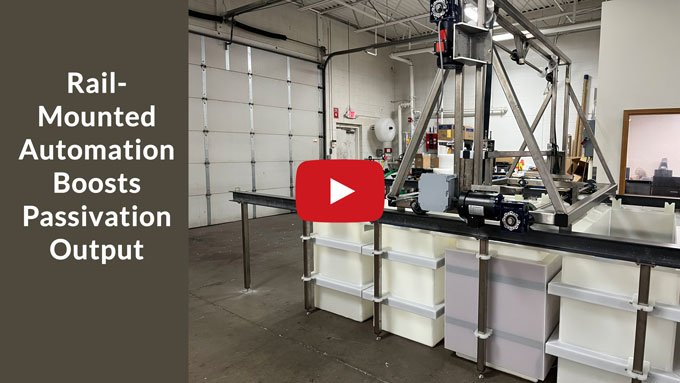
Automated Passivation System for High-Volume Production
Built with large-volume polypropylene tanks and fume-resistant components, including robust 304 stainless steel framing and a fiberglass I-beam, our system stands resilient against harsh chemicals, assuring superior chemical durability and equipment longevity.
By anchoring the automation’s structural supports directly to the tanks, we deliver a stable and efficient operation that ensures your production line is always ready to perform at its best. This integrated design enables the system to monitor readiness by checking that fluid temperatures are met, and the line is prepared to start receiving components into the passivation system for processing.
Rail-Mounted Gantry Automated Passivation System
Automated Passivation System Features
Experience enhanced productivity and safety with our Automated Passivation Systems:
- Integrated Automation: Our system eliminates the need for cumbersome overhead cranes, offering seamless operation and control through a single PLC controller. This integration ensures your system is always primed for action, maximizing efficiency. With a single point of access, the PLC controller enhances operational safety by reducing complexity and ensuring precise system control.
- Customizable Load Capacity: With a standard capacity of up to 300 lbs. per load and the option for customization up to 1000 lbs., our system adapts to your specific project needs, accommodating a variety of load sizes and applications.
- Flexible Operation Modes: Choose between fully automated and manual modes to suit your production requirements.
- Fully Automated: In fully automated mode, the system follows pre-programmed recipes, moving baskets or racks through the process according to specified times and conditions. This mode is ideal for consistent, high-volume production.
- Manual: In manual mode, an operator can manually control the movement of baskets or racks using a joystick, allowing for more hands-on management of the process. This mode is beneficial when specific adjustments are needed during production.
- Advanced Safety Features: Prioritize safety with features like e-stop cords, hard stops on I-beams, and pinch guards. Safety light curtains are also available as an option. Low-level sensors in the tanks ensure that equipment does not run without adequate liquid level. These elements create a secure working environment, protecting your operators and ensuring peace of mind.
- Multiple Load Processing: Our compact gantry rail system processes multiple loads simultaneously, optimizing throughput and reducing space requirements compared to traditional systems. While one load is passivating, another load can be cleaned and dried, skipping over the passivation in progress. This allows for greater throughput and higher production volumes.
- Flowlines: Larger diameter pipes allow for faster filling of tanks, increasing efficiency. Rinse tanks can be connected to an RO (reverse osmosis) or DI (deionized) water source, such as a DI skid.
- Automated Tank Filling: The automation system uses flow restrictors and solenoid valves to automatically control the filling process, eliminating the need for manual tank filling by the operator.
- Advanced Monitoring: The conductivity meter in the final rinse ensures that rinse water remains fresh, and automatically triggers the addition of more water when needed. Similarly, the pH meter in the passivation tank monitors the passivation solution and triggers the addition of more passivation solution as needed.
- Flowing Rinses: Rinse tanks use an overflow weir when adding water, so the water at the top of the tank is emptied first, while new fresh water enters from below. This essential feature helps maintain the freshness of the rinse water after each rinse.
- Efficient Drying: Air knife drying tank uses a regenerative blower with warm air for high amounts of air at low pressures, for clean, contaminant-free drying.
- Chemical Compatibility: Built tough with fume-resistant components, our system withstands harsh chemicals, ensuring long-term durability and reliability in demanding environments.
- Load and Unload Carts: Streamline your workflow with wheeled load and unload carts, facilitating easy handling of baskets or racks. Extra carts are available for staging, ensuring continuous operation. Operators are not required to lift any items, minimizing physical strain and enhancing overall efficiency.
- Single-Button Start: The operator can start the next load by simply moving the next cart into the loading position and pressing a single button once the PLC is programmed.
- Racks or Baskets: Tailor the system to your needs with options for racks or baskets, providing flexibility based on part requirements. Racks prevent contact between parts, while baskets allow for bulk processing.
These features make Best Technology’s Automated Passivation Systems a robust solution for high-volume production, delivering efficiency, safety, and reliability.
Learn more about automation benefits on our page What is Process Automation for Metal Finishing?
Automated Passivation System with Basket
Automated Passivation FAQs
-
Why are automated systems easier to process validate than manual equipment?
Process control and stability are critical aspects to regulated medical device and aerospace processes. It is important to ensure that a process has input and output variable limits which are defined and fully tested during process design, Equipment Qualification (IQ), Operational Qualification (OQ) and Process Qualification (PQ) validation testing. Setting up a proper DOE (Design of experiments) to test these limits is also important as the results of the DOE will give statistical confidence intervals of the limits. Being that operators and employees perform various process operations different no matter how instructed in work instructions, the variation of operators must also be captured during process qualification (PQ) validation. An automated system typically eliminates many of the operator variability in the manufacturing process and this process “input” elimination also allows for tighter process output controls. For example, in our automated passivation system, the elimination of relying on an operator to move the parts basket from stage to stage ensures that the parts remain in the appropriate (wash, rinse, acid passivation, etc) solutions for the process defined times and in accordance with the proper ASTM A967, AMS2700, etc specification. If a parts basket is immersed in the acid passivation solution too short or long duration, the passivation can likely fail and be outside specification limits.
-
Do you need any agitation beyond ultrasonics during the cleaning or passivation process with an automated system?
Our automated cleaning and passivation system includes in-process tank circulation which agitates the solution, alternating between ultrasonics (as fluid movement dissipates ultrasonic energy). This also allows the process tank to filter solution back in the storage tank.
-
In an automated system, are there contamination issues when you pump solutions out of the main processing tank?
Many of our automated cleaning and passivation systems pump the cleaning, rinsing and passivation acid solutions between tanks, unlike a traditional system where the parts are moved from tank to tank.
To reduce any contamination issues, we mount rinse spray nozzles in the cover of the system to rinse down the parts and tank walls. All the plumbing to and from the process tanks is separated to further reduce any contamination. This results in less contamination compared to the drag-out that occurs from moving parts from tank-to-tank in a traditional multi-tank setup.
-
What is the industry standard for acceptable particle count after cleaning or passivation?
Acceptable particle counts depend on the specification which the parts are processed to: ASTM A967, A380, F86, AMS 2700, etc. For passivation, DI rinse water is recommended for best results.
Our automated systems offer conductivity meters which monitor water quality and total dissolved solids. The storage tanks have facility DI water source needle valves which open when conductivity limits are not met. This allows for a continual overflow of the rinse tank until rinse water specifications are reached.
-
What are the pros and cons of pump-based systems vs. rail-mounted gantry crane automation?
Pump-Based System
-
Lower System Cost: Typically less expensive to purchase and install.
-
Simplified Maintenance: Fewer moving parts reduce the risk of mechanical failure and simplify upkeep.
-
Compact Footprint: Takes up less space on the production floor.
-
Flexible Tank Placement: Storage tanks can be located outside of the cleanroom or processing area.
-
Closed-Loop Operation: Minimizes operator exposure to chemicals, improving safety and compliance.
Cons:
-
Longer Cycle Times: Requires time to fill and drain the process chamber (typically ~2 minutes each).
-
Single-Basket Workflow: You must wait for the entire cycle to finish before processing the next batch.
-
Process Limitations: Not compatible with pickling or descaling applications.
Rail-Mounted Gantry Crane Automation
-
Higher Throughput: Multiple baskets can be processed in succession, increasing production capacity.
-
Scalable Design: Systems can be built much larger to handle high-volume needs.
-
Supports Pickling/Descaling: Capable of handling aggressive chemical processes.
-
Faster Cycles: No fill or drain steps—parts move through already-filled process tanks.
Cons:
-
Higher Initial Cost: Requires more infrastructure and automation.
-
Larger Footprint: Occupies more floor space compared to pump-based systems.
-
Increased Maintenance: More mechanical components introduce additional maintenance needs.
-
Common Applications for Automated Passivation Systems
Our Automated Passivation Equipment excels in industries demanding high-volume production with stringent quality standards. Ideal for aerospace, medical devices, and electronics sectors, our systems ensure precision and reliability. With the ability to handle various load sizes and applications, they offer a versatile solution for diverse industrial needs.
Our automated passivation system is specifically engineered for high-volume stainless steel passivation in compliance with industry standards such as ASTM A967, AMS 2700 and ASTM F86. It supports the following methods:
- Nitric acid passivation type 1, 2, 3, 4 with sodium dichromate
- Citric acid passivation type 1, 2, 3, 4 & 5 using CitriSurf®, or other citric acid solutions such as Esma E964 Citric Deox
CitriSurf® is a registered trademark of Stellar Solutions, Inc. McHenry IL USA.
Other Applications
Best Technology’s automated systems are not only ideal for high-volume production with passivation, but also perfectly suited for a wide range of other chemical processing applications.
- Chem Film / Alodine / Chromate Conversion Coating
- Electropolishing
- Ultrasonic Cleaning / Precision Cleaning
- Phosphate Coating
- Pickling, Descaling and Etching
Common Configurations
Automated passivation systems for high-volume production offer great flexibility in sizing. Each system is custom-built to the requirements of your application. Tank size range can be from 50 gallons to hundreds of gallons, and is highly customizable.
Standard load capacity for baskets is 300 lbs., but can be higher based on project requirements. Racks and extra baskets are also available.
Excellence in High-Volume Automated Passivation Systems
Elevate your production efficiency with Best Technology’s Automated Passivation Systems. Contact a passivation expert today to discover how our customizable solutions can be tailored to meet your specific requirements and transform your manufacturing process.